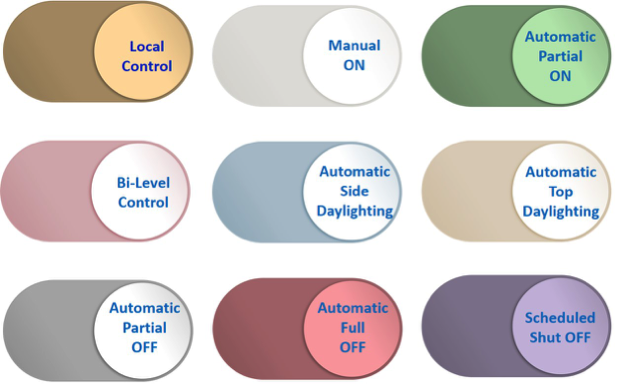
Will Your Lighting Controls Really Save Energy?
July 18, 2018
By Sonya M. Pouncy, CEM, CMVP, LEED-AP. Sonya is a senior engineering consultant with Energy Sciences. The firm helps clients meet energy challenges with practical solutions that reduce waste and increase net operating income.
If they are Michigan Energy Code (MEC) compliant, the answer is yes. The new MEC, effective as of September 2017, brings with it more than 100 updates developed to improve building energy performance. Since lighting can represent 30% or more of your commercial building’s energy use, many of the changes are related to the lighting system. One of the more significant revisions pertains to lighting system controls.
The MEC, which is rooted in ASHRAE 90.1-2013, includes 9 basic control schemes for interior lighting and 3 for exterior lighting. The strategies are designed to reduce the use of electric lighting when areas are unoccupied or when there is sufficient natural lighting. Control schemes apply to all interior spaces—even manufacturing high bay areas—as well as parking garages and other exterior areas. Depending on the space function, some schemes are required; others are the designer’s choice. For example, with stairwell lighting, in addition to having strategies for bilevel, daylighting and vacancy control, the designer must also choose between Automatic Full OFF or Scheduled OFF control.
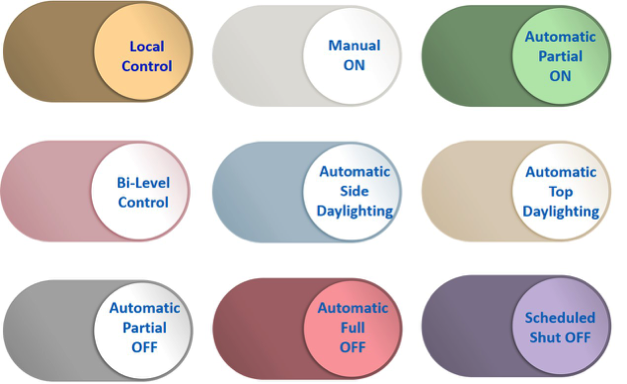
One mandatory provision of the new Michigan Energy Code is the use of one or more Strategy for Interior Lighting Control depending on space function.
Lighting controls, particularly those for daylighting, can be challenging to get just right. Often factory setpoints need to be adjusted to accommodate field conditions. This may involve multiple trips to the jobsite under varying daylight and occupancy conditions to optimize system operation. To ensure that new controls are programmed and calibrated to function correctly, the MEC requires that the operation of all installed lighting controls be tested in situ. Functional testing includes quality control checks such as confirming that lighting power levels modulate appropriately within the allotted time; that lights are not inadvertently activated by movement in nearby areas or by HVAC equipment; and that daylight controls have appropriate threshold levels and floor area coverage.
The MEC also requires that the “individual responsible for the functional testing shall not be directly involved in the either the design or construction.” If you’ve ever diligently proofread a paper you wrote only to have a teacher point out 3 or 4 glaring errors, you know it can be challenging to check your own work. That’s why the MEC requires that commissioning be performed by a disinterested party—someone other than the designer or installing contractor. Not only does this third-party testing bring fresh eyes to the project, but it also adds a degree of objectivity which can go a long way in ensuring that your project provides the lighting quality, quantity and energy savings it was designed to deliver.
To improve the overall indoor environmental quality and energy performance of your building, add detailed commissioning criteria to the bid documents for your next lighting project. For best results, be sure your commissioning specification explicitly describes test requirements for occupancy sensors, daylight responsive sensors and automatic time switches. And, to ensure that your facility management staff will be fully prepared to operate and maintain your new lighting system, be sure to include specific requirements for system documentation and building operator training. By following these best practices, you’ll provide your O&M team with the tools they’ll need to operate and maintain your new lighting system for optimal performance throughout—and maybe even beyond—its design life.